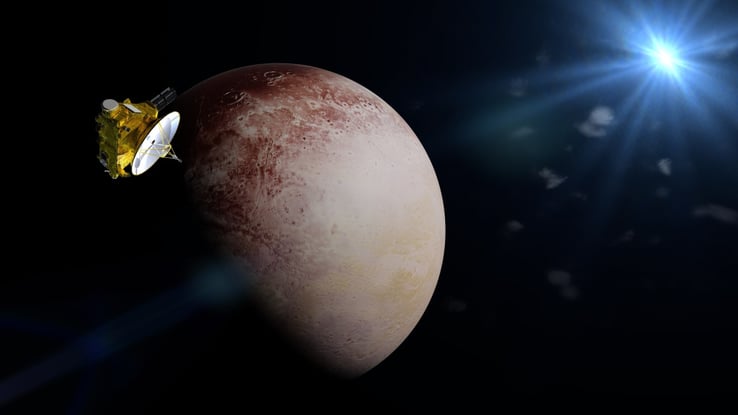
But what are the main causes of this frequency error, and what should we be looking for in our oscillators to ensure high levels of systems performance?
Main Causes of Frequency Error
There are four main drivers that cause frequency error in oscillators:
- Crystal aging
- Frequency vs. temperature
- Frequency vs. supply
- Frequency vs. load
Of these four drivers, crystal aging is one of the most common failure modes. Very plainly, crystal aging is used to describe long-term frequency change that happens over time caused by changes in either the environment or the crystal itself. A good analogy would be breaking in a new pair of dress shoes. The fit will change more rapidly at the beginning, but eventually they'll settle in and feel great!
There are two types of Crystal aging, positive aging and negative aging. Positive aging occurs when contaminants are driven out of the quartz crystal. Conversely, negative aging occurs when contaminants are driven into the quartz crystal.
How Crystal Aging Is Measured
So how is crystal aging measured, and what are frequency control experts doing to make sure it doesn't become a problem in the system down the road?
Performance requirements related to crystal aging are maintained to a mil-spec published by the US government. The typical process to meet an aging requirement is to perform a burn in on the oscillator, put the parts into a aging system where it is measured multiple times a day, and then plot and compare these measurements against the mil standard on crystal aging.
Using these measurements, frequency control manufacturers can project the aging rate of their devices over the entire life span of a system up to 20 years and beyond.
Contamination as a Crystal Aging Factor
There are many factors that can affect crystal aging rate. Chief among these is the amount of contaminants that become sealed inside the resonator's package. As you can imagine, inside an oscillator package are several interface boundaries between electrical connections, mechanical connections, and the crystal blank itself. Each one of these interfaces is an opportunity to introduce new contaminants into the package.
Potential sources of out-gassing or contamination can be found in the materials that make up the resonator itself. In fact, the very act of sealing the package can also introduce unwanted sources of contamination. For example, quartz is a getter and readily absorbs moisture, which is extremely detrimental to a vacuum-sealed package.
That's why humidity is tightly controlled during the manufacturing process of high quality frequency control devices. Some common steps to avoid excess moisture include storing and processing components in nitrogen dry boxes, hydrogen firing, and sealing the final resonator under high-vacuum and at elevated temperatures.
For instance, on the BG61 oscillator that is flying on the New Horizons spacecraft currently exploring Pluto, the crystal was held under high-temperature vacuum for about a week prior to being sealed under high-vacuum. The BG61 is widely recognized as the most stable crystal in the UNIVERSE! Curious to know just how stable that is... well, it's 0.0001 ppb or 0.0000000000001 parts per billion. Speaking of billions, Bliley's ultra-stable crystals are now 5 billion miles from earth!
TIP: Reduce Temperature Range to Improve System Performance
So, what can designers do to insulate themselves from the negative effects of crystal aging? One counter-intuitive design approach is to reduce the required temperature range for the oscillator.
A common systems engineering approach is to build margin into your component selection to ensure system level performance. If a system must operate across a temperature range from -20 to 70 degrees C, it's natural for a systems engineer to say "I'm going to buffer myself and spec the oscillator over the full temperature range -40 to 85 degrees C."
The engineer thinks they'll get a better part since it will be able to operate over an extended temperature range. However, this forces the frequency control manufacturing to ensure their component must operate at up to 95C. These elevated temperatures will accelerate aging (increasing the frequency error) and lower the devices MTBF or mean time between failures.
What began as an attempt to get a superior performing part ends with getting a part that has sub-par performance and will likely have a reduced operational life.
Connect Deeper
The next time you're designing in a crystal, OCXO, VCXO, or TCXO, remember the effects that aging has on overall clock performance and ways you can compensate within your design.
If this article resonated with you (yes, that's a frequency control pun) follow us on LinkedIn, Facebook, or Twitter to catch more information like this!
[Editor's note: This article was originally published on May 9, 2016 and updated on November 23, 2022.]