Poor manufacturing environments can significantly reduce the performance quality of a pressure transducer. A failing pressure transducer will lead to problems with sensors and will provide inaccurate readings (or none at all).
A faulty pressure transducer can not only cause frustration and waste time, but it can also lead to unnecessary costs.
To prevent pressure transducer problems or failure from happening in the first place, let's take a look at seven pressure transducer troubleshooting methods to keep your transducers and sensors working great!
7 Incredibly Effective Ways to Prevent Pressure Transducer Problems
1. Eliminate Shock and Vibration
Much like crystal oscillators, transducers have been known to take a heavy beating from various sources of shock and vibration. Frequent problems that can arise include:
- Broken circuit boards
- Dented enclosures
- Disconnected wires
- Faulty signals
- Intermittent problems
- Shortened life span
The first step to solving a shock and vibe problem is to prevent it from happening in the first place.
A simple solution is to install the transducer as remotely as possible from any obvious sources of shock and vibrations. In some cases, shock and vibration isolators can be used.
Also be sure to choose an experienced and trusted transducer manufacturer that can design your transducers and blanks to be as shock and vibration resistant as possible.
2. Control the Temperature
There are many components in transducers that must operate under specified temperature ranges. High temperatures or high deviations in temperature are common reasons for pressure transducer problems.
Again, failing to be mindful of the location of the transducer is a frequent mistake made by installers. Incorrectly placing a transducer near hot steam lines, someone welding, or other sources of heat can easily lead to inaccurate sensor readings and performance.
3. Avoid Electrical Disturbances
The job of pressure transducers is convert pressure into a recordable electrical signal. During that conversion process, exterior electrical disturbances or emissions can naturally influence the original signal.
Electromagnetic or radio frequency interference (EMI/RFI) can be attributed to sources like:
- Power lines
- Computers
- Walkie talkies
- Cell phones
- Large machinery that produce magnetic fields
Transducer manufactures play a key role when it comes to preventing this problem waiting to happen. Specific RF design considerations should be used to prevent EMI/RFI impacts.
Shielding, filtering, and suppression should be used in the transducer's design to help eliminate electrical disturbances. Contacting the transducer manufacturer to make sure these are incorporated into the design is recommended.
4. Prevent Voltage Spikes
Along the same lines as electrical interference, even the smallest spikes in voltage input could lead to bad news for your pressure transducer or sensors. High-energy voltage spikes that last even a millisecond can cause damage.
The worst part is that voltage spikes are very difficult to track unless the source is easily distinguishable (such as lightning). Manufacturers using the transducer must be very aware of the entire manufacturing environment to prevent and reduce voltage spikes.
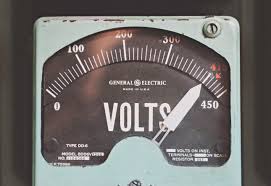
Trusted transducer suppliers apply specific techniques to prevent voltage spikes from damaging or hindering the performance of your transducer and sensor. Make sure to speak with the supplier to be sure this process is applied beforehand. The supplier can also help determine the source of your current voltage spikes. (If you haven't caught on yet... make friends with your supplier!!)
5. Optimize Your Lighting
Yes, even the lighting in your facility can lead to pressure transducer failure. (Welcome to a life of an engineer... a new problem everywhere you look.)
Luckily the solution is pretty straight forward: avoid fluorescent lighting.
Fluorescent lighting:
- Requires an initial high voltage to start the electrical arc when turned on — significantly higher than other lighting options. The initial high voltage can lead to voltage spikes in nearby transducers.
- Produces an electromagnetic field that can interfere with the original signal created by the transducer.
The takeaway: avoid using transducers underneath or near fluorescent lighting.
6. Don't Overpressure
Be aware of overpressure. A common cause of overpressure is a phenomenon called water hammer. This is a pressure burst that can result in permanent diaphragm damage, causing a false sensor reading.
Understanding the dynamics of your system and the limits of your transducer are important ways to prevent overpressure problems.
The design and installation of the transducer must carefully take into account its interaction with:
- Pumps
- Control valves
- Balancing valves
- Check Valves
- Pressure switches
- Motors
- Compressors
7. Understand Random Failure
After a successful installation of a transducer and sensor, both will experience an increase in natural "random failure rates" over time.
The random failure rate of a transducer or sensor is commonly calculated by referencing the mean time to failure (MTTF). The MTTF is directly related to the design of the product, which includes:
- The number of components
- The complexity of components
- Applied stress levels
A calculated MTTF of 100 means that if you have 100 units of this product operating under the same conditions, you can expect one of them to fail per year as a result of random component failure.
The #1 Way to Prevent Pressure Transducer Problems
The most common cause of pressure transducer and sensor failure is that the wrong transducer is being used for a specific job. This is why it's so important to discuss all of the design considerations above with an experienced transducer supplier. They'll be able to ensure the transducer is accurately designed for your manufacturing environment and needs.
Bliley Technologies has been a trusted manufacturer of transducers and specialty blanks for over 90 years. We take into account all of the best practices to supply some of the highest quality transducers and blanks on the market today.
Contact us with your specific transducer needs and requirements and we'll be sure to find the best solution for you and your company!